Predictive Maintenance at Unilin Group: Leveraging Online Vibration Monitoring and Anomaly Detection
The Unilin Group, part of the larger Mohawk International, is a major player in the European construction and building materials market. With over 30 factories across Europe, Unilin specialises in flooring, insulation materials, and boards used in furniture manufacturing. In a this interview, Kurt Dhaene, one of the Group Reliability Managers at Unilin, shares his insights into the company’s transition towards data-driven maintenance and the implementation of predictive maintenance technologies.
A Glimpse into Unilin’s Operations
“Unilin is part of a bigger organization, Mohawk International, but focuses mainly on the European and part of the Asia/Pacific market,” explains Dhaene. “We provide several materials used in construction and buildings, including laminate and PVC floor coverings, insulation materials, and boards for furniture manufacturing.”
Unilin’s commitment to innovation is evident from its approach to maintenance. Kurt’s role as Group Reliability Manager involves supporting projects across various plants to increase reliability. “We don’t work for a specific plant; instead, we are part of the group organization. We use competence centres to increase the maturity of our plants. My competence centre does that by focusing on using digital tools to reduce repair time and support the transition from preventive to predictive maintenance,” says Kurt Dhaene.
Drivers of Transitioning to Predictive Maintenance
Several factors drive Unilin’s shift towards predictive maintenance. “The typical driver is, of course, reducing costs while maintaining reliability, but equally important are increasing safety and supporting sustainability objectives,” Kurt emphasises. Using materials as efficiently as possible and minimizing energy use are key components of Unilin’s strategy to balance asset utilization with cost control while contributing to a more sustainable world.
Current Status of the Digital Transition
Unilin’s journey towards predictive maintenance is well underway. Kurt Dhaene describes their approach: “We develop our initiatives as products, focusing on reusability. Thus we can scale successful pilots across multiple plants.” Some of these products have already moved beyond the pilot phase and are being rolled out across other facilities. For instance, Unilin has implemented systems that transfer data from PLCs to their SAP system, triggering preventive maintenance plans based on real-time data.
One of their notable projects involves monitoring the lifetime of knives in chippers used for breaking down PVC materials and wood. This system analyses the current drawn by the chipper, the hydraulic pressure, and the material levels in the storage to determine the optimal time for knife replacement, thus avoiding unnecessary downtime and promoting sustainability.
The Role of Vibration Monitoring
Unilin has been collaborating with I-Care to implement remote vibration monitoring, a crucial element of their predictive maintenance strategy. “We already have between 100 and 150 vibration sensors installed in our plants,” says Kurt. Initially, these sensors were used to set fixed alarms for vibration levels. However, this approach proved inadequate for equipment with variable loads and speeds.
To address this, Unilin combined vibration data with other process data from PLCs to create context-aware detection algorithms. “We teamed up with Yazzoom, which provided an anomaly detection product. By combining data from I-Care’s vibration sensors with process data, we trained models to detect anomalies more accurately,” Kurt Dhaene explains.
Monitoring Thermal Oil Pumps
Unilin chose to focus on thermal oil pumps for this project. These pumps are critical, and Unilin already had historical data from existing sensors. “We selected thermal oil pumps because they are relatively simple, and we had the necessary information about their components,” Dhaene notes. I-Care’s sensors vibration signals are converted into meaningful information , so called features, which Yazzoom’s system analyse to detect deviations from normal operating conditions.
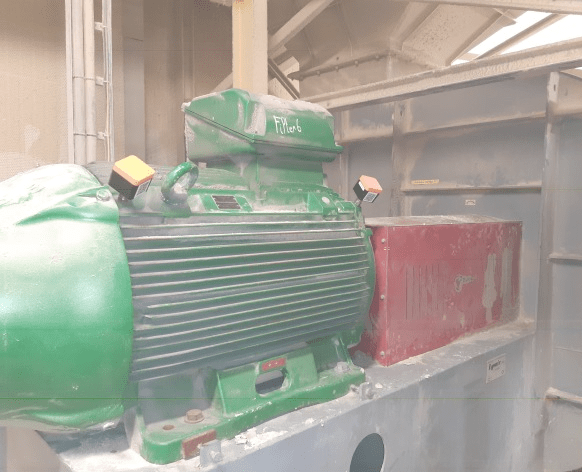
This integrated approach has yielded promising results. “The system runs on 15 primary pumps, and sometimes it detects problems other or faster than our monitoring specialists. It’s very sensitive to different modes of operation,” says Dhaene. However, there are occasional detections that require further investigation by vibration specialists, which highlights the need for continuous model training and refinement.
Benefits and Challenges
This system yields clear benefits “It allows us to detect failures much earlier and more accurately than before. This early detection enables timely preparations and prevents unexpected downtime,” Kurt Dhaene explains. For instance, redundant pumps can be activated swiftly, ensuring continuous operation.
However, the transition to predictive maintenance is not without challenges. Kurt emphasized the importance of human expertise in interpreting data. “There’s an exponential increase in information available from equipment. The challenge is detecting meaningful signals and getting this information to the right person at the right time,” he says.
Collaboration with I-Care and Yazzoom
Unilin’s collaboration with I-Care has been instrumental in their success. “I-Care provides high-quality sensors and has the mechanical and IT knowledge to support us. This combination was crucial for us,” Dhaene notes. The ability to interpret vibration signals and connect them to IoT systems for anomaly detection was a key factor in choosing I-Care as a partner.
Yazzoom was chosen as a partner because their product Yanomaly provides not only a number of generic models, but also detectors that align well with our types of equipment and are easy to scale. Moreover, they were willing to work together to make this integration a success.
The Human Element
The transition to digital, data-driven maintenance relies heavily on human expertise. “Data specialists and system experts are essential. It’s about getting the right information to the right person at the right time,” Dhaene emphasized. Vibration analysts, for instance, need detailed information to make informed decisions, while operators and technicians require interpreted data translated into actionable insights.
In conclusion, Unilin’s journey towards predictive maintenance highlights the importance of integrating advanced technologies with human expertise to enhance reliability, safety, and sustainability. Their collaboration with I-Care and Yazzoom serves as a model for how companies can leverage data-driven tools to achieve significant operational improvements.
The insights gained from Unilin’s predictive maintenance projects will be presented at the Asset Performance 2024 conference in Antwerp, Belgium, this November. Mr. Tom Rombouts of I-Care and Mathieu Vroman from Unilin will explore the synergies between online vibration monitoring and anomaly detection in predicting equipment failure, focusing on enhancing asset management practices. They will showcase how Unilin collaborated with Yazzoom and I-Care to monitor their fleet of thermal oil pumps.
Don’t miss the opportunity to learn from their experience at the Asset Performance 2024 conference. Register now and be part of the conversation shaping the future of asset management.